United by Metal Fabrication: Why United Alloy Chooses CI
In 1999, United Alloy (UA) was founded in Janesville, Wisconsin. That same year, the company welcomed its first Cincinnati Incorporated machine, a 135-ton press brake.
The company has grown steadily since. They got their start in a 20,000 square foot facility and currently reside in a 350,000 square foot space. UA also recently opened a 121,000 square foot facility in Texas, which houses trusted CI equipment as well.
We caught up with Luke R. Jaynes, President of UA, and Jerry Clark, Mechatronics Manager, to talk about United Alloy and how CI has helped them grow.
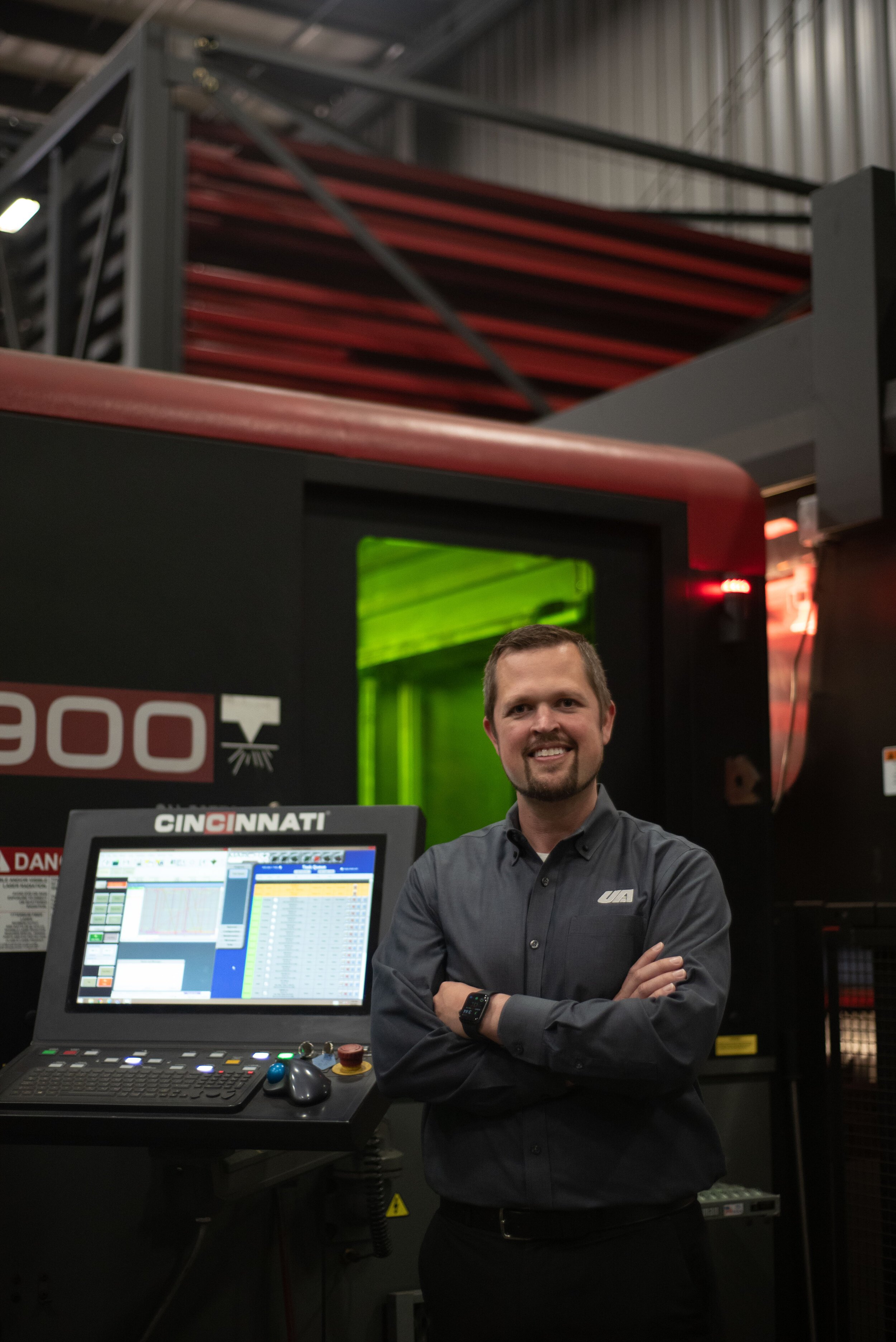
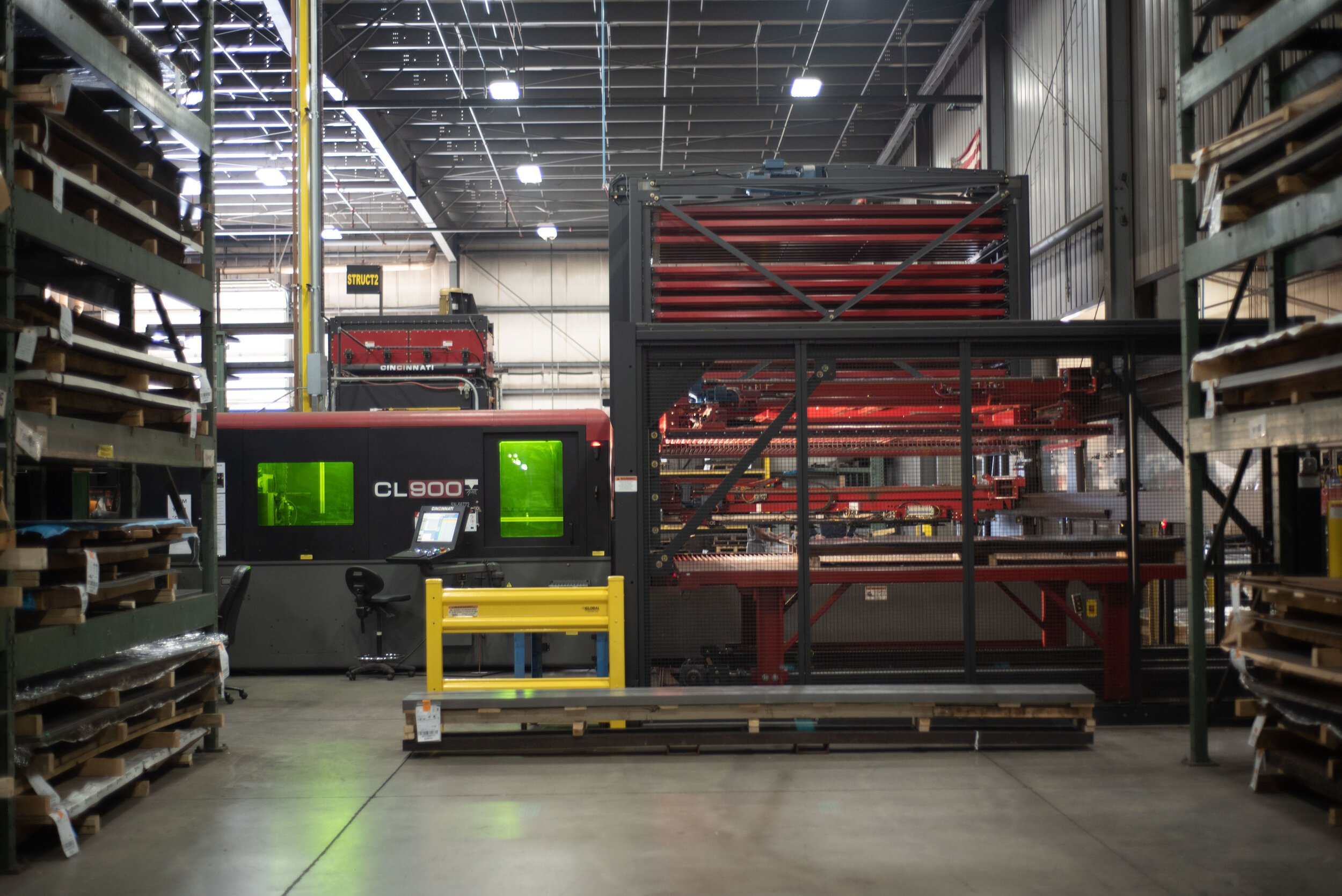
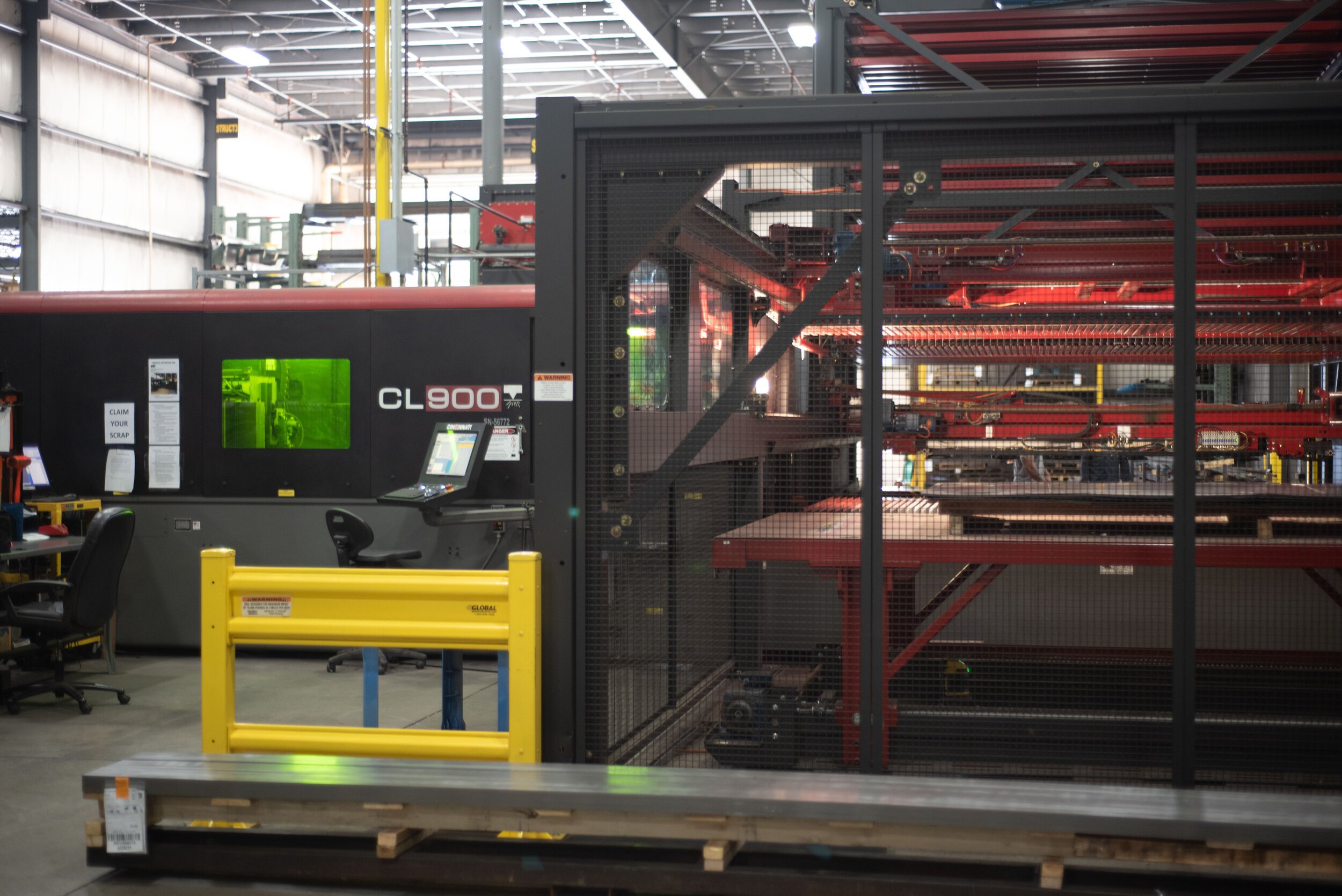
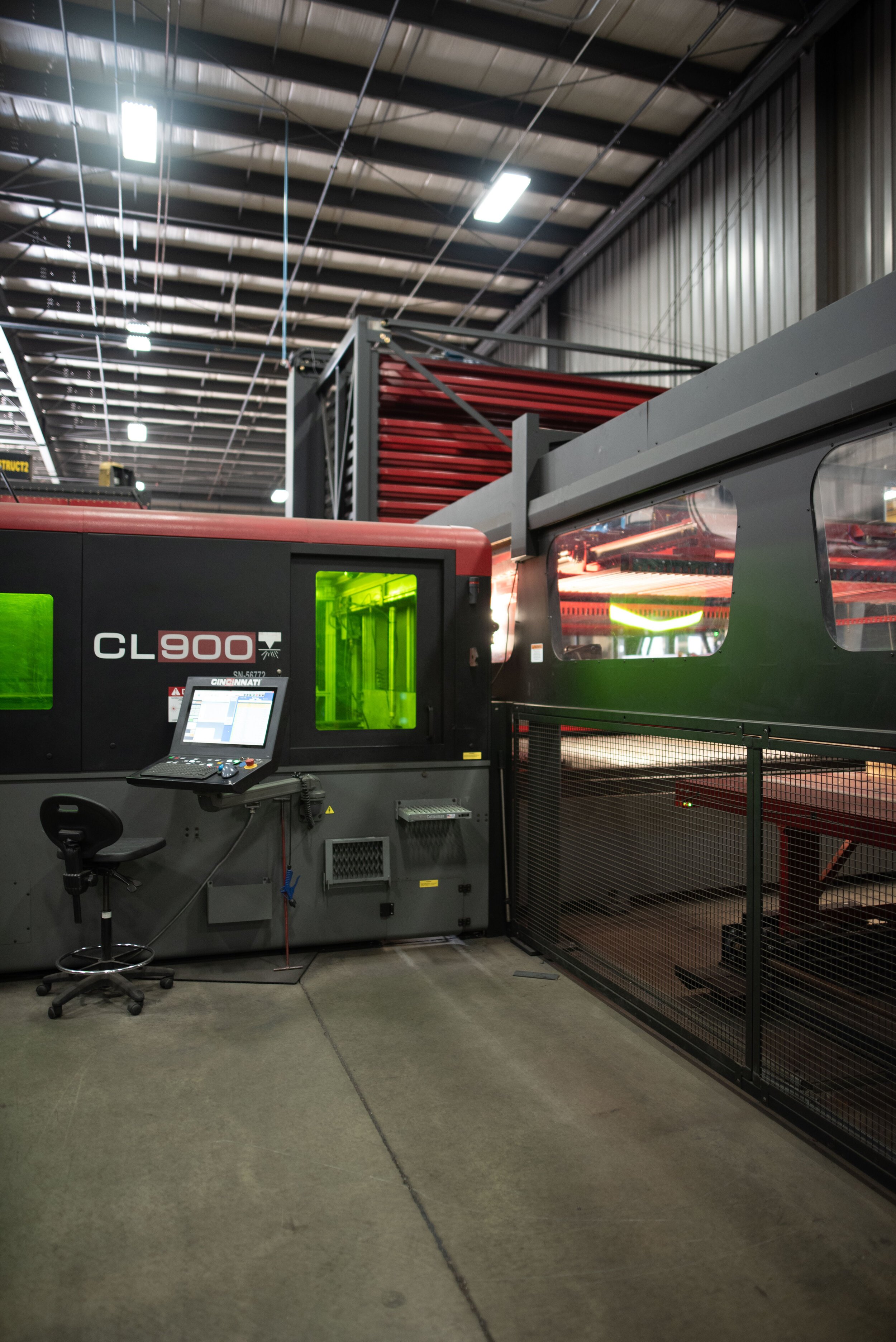
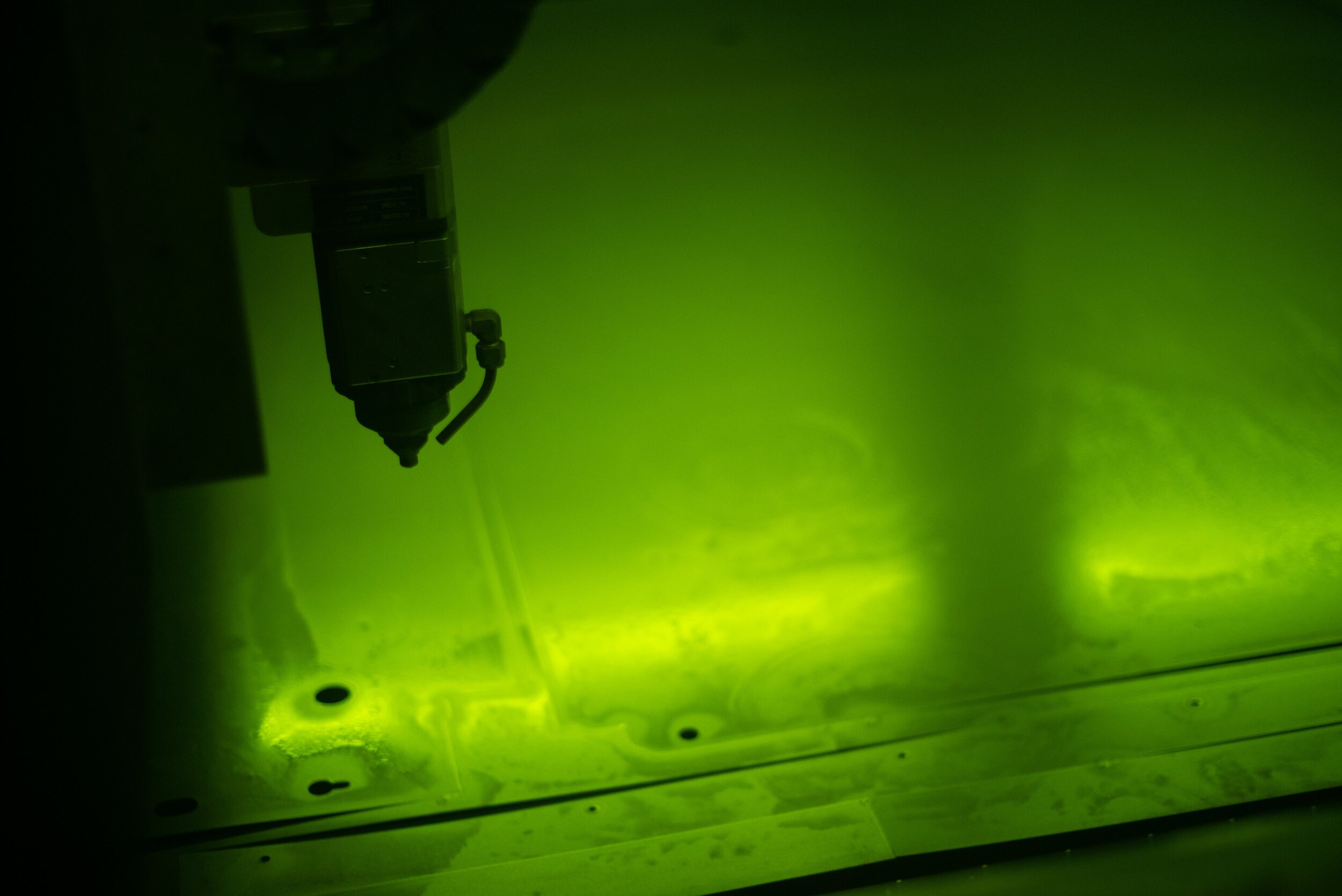
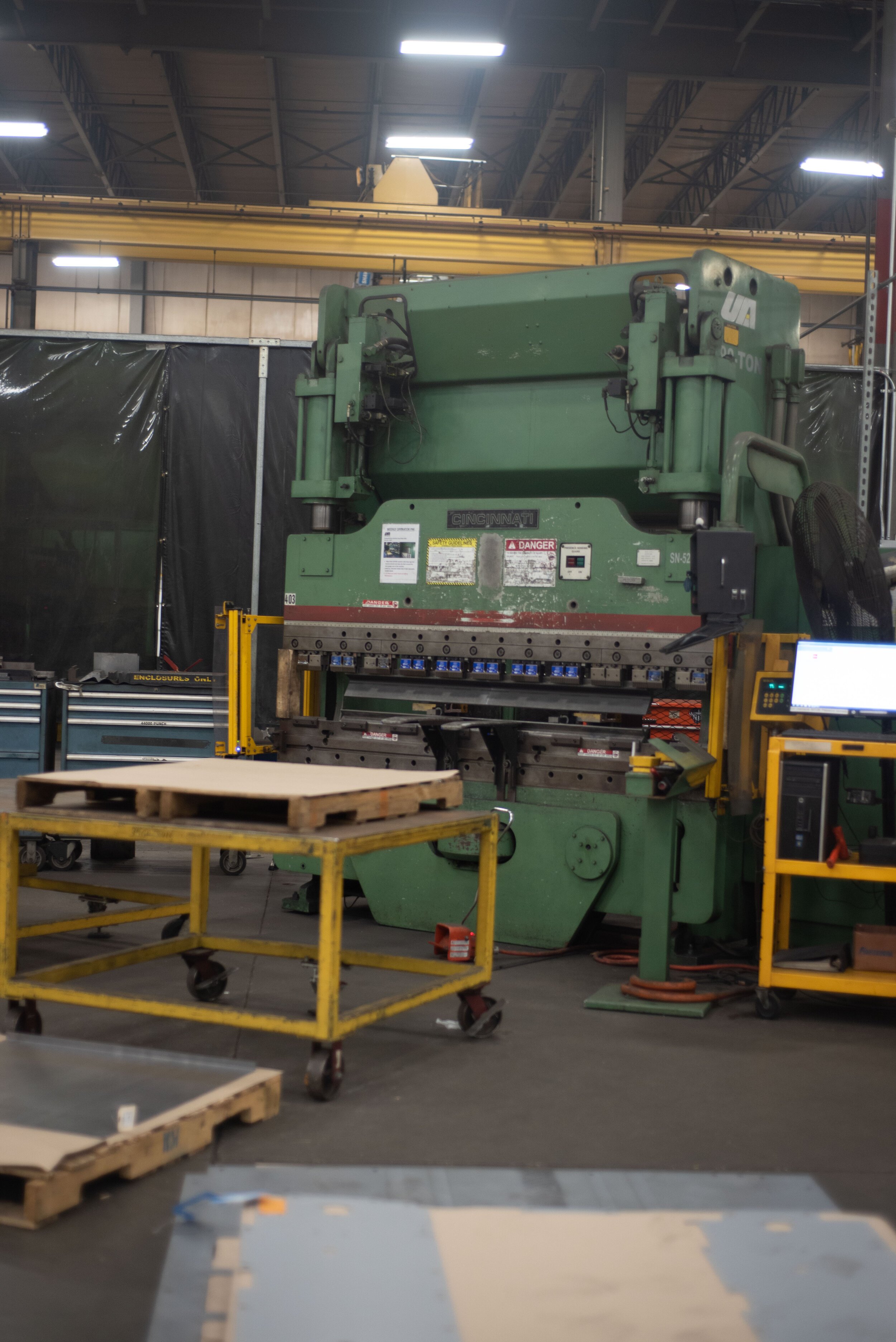
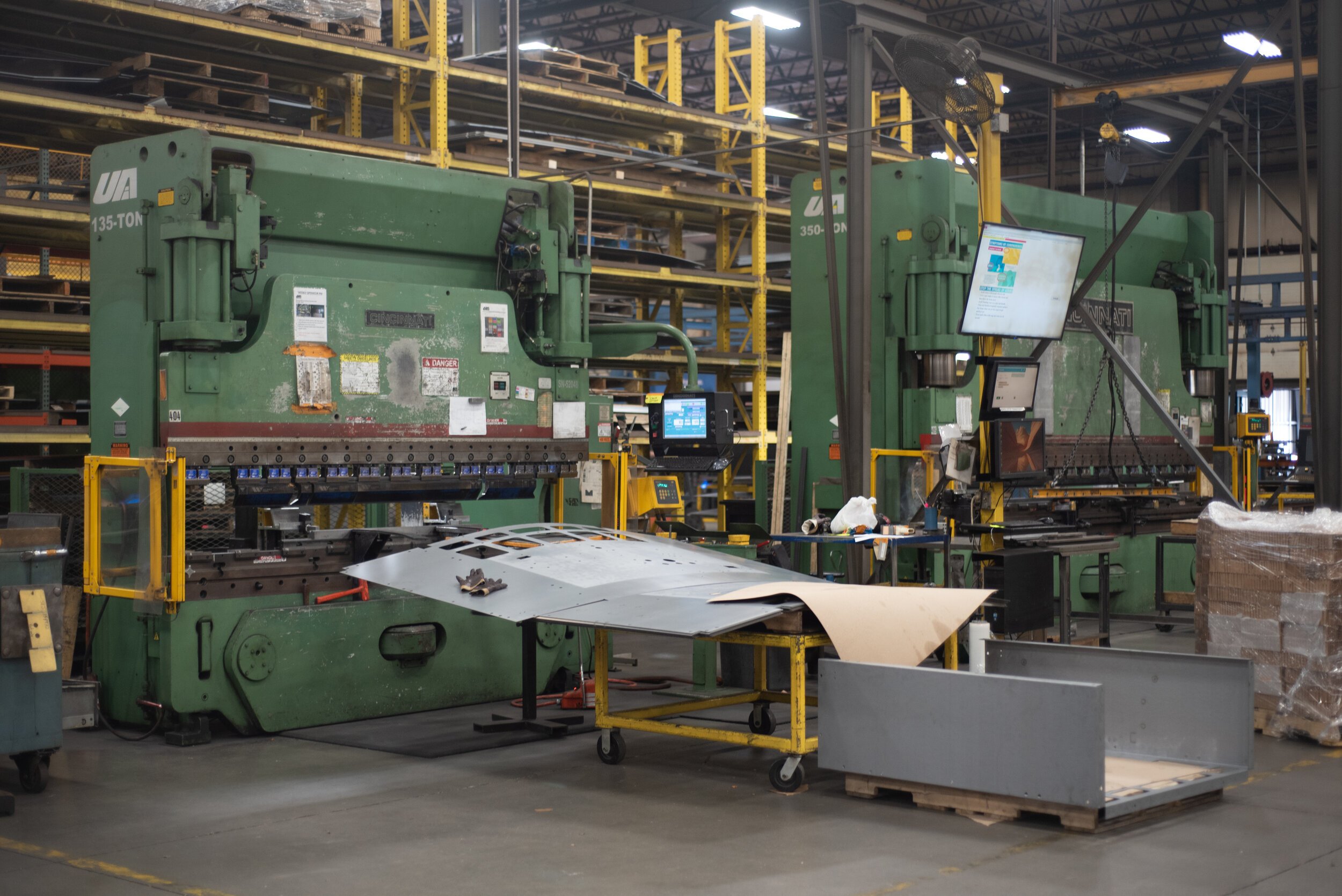
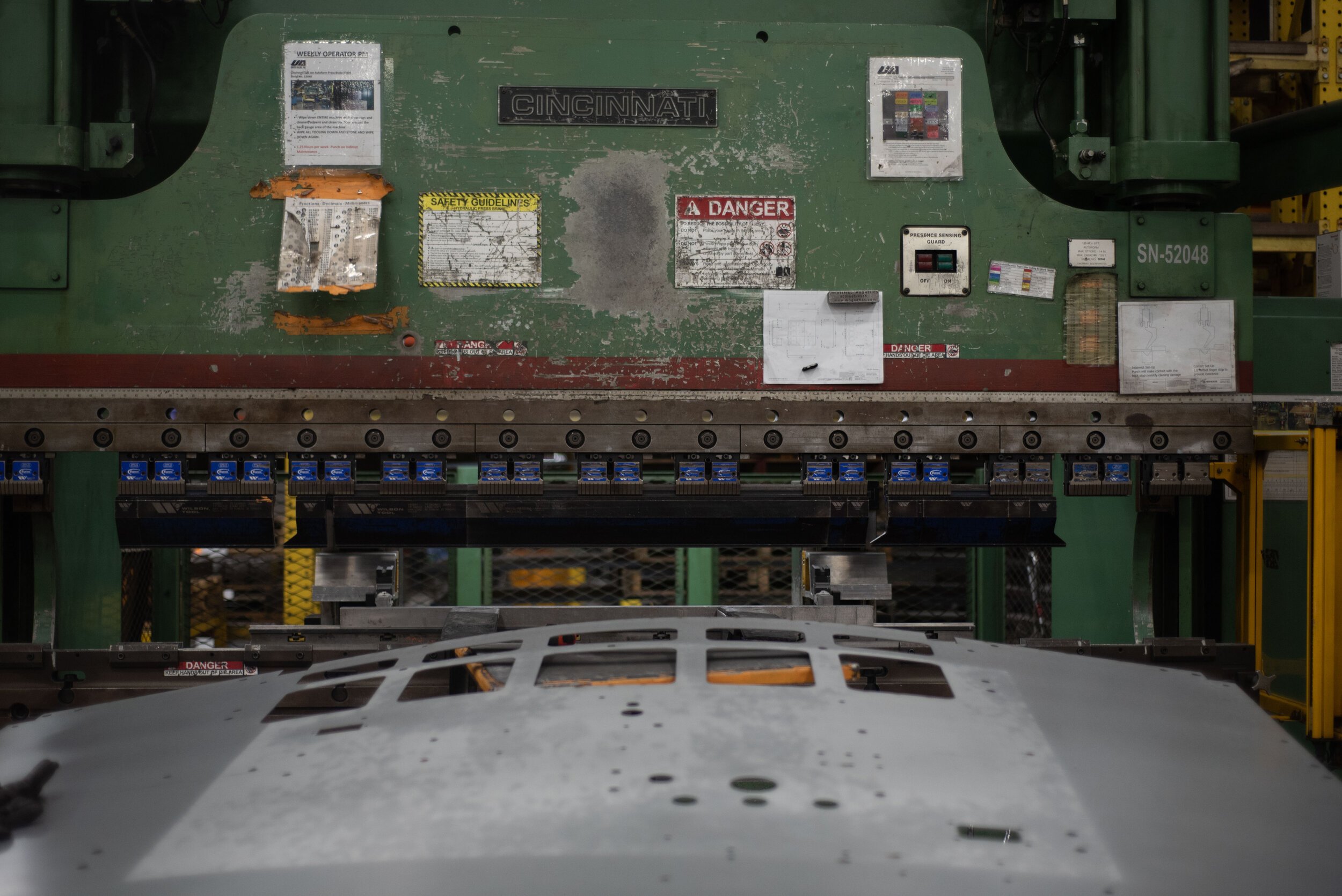

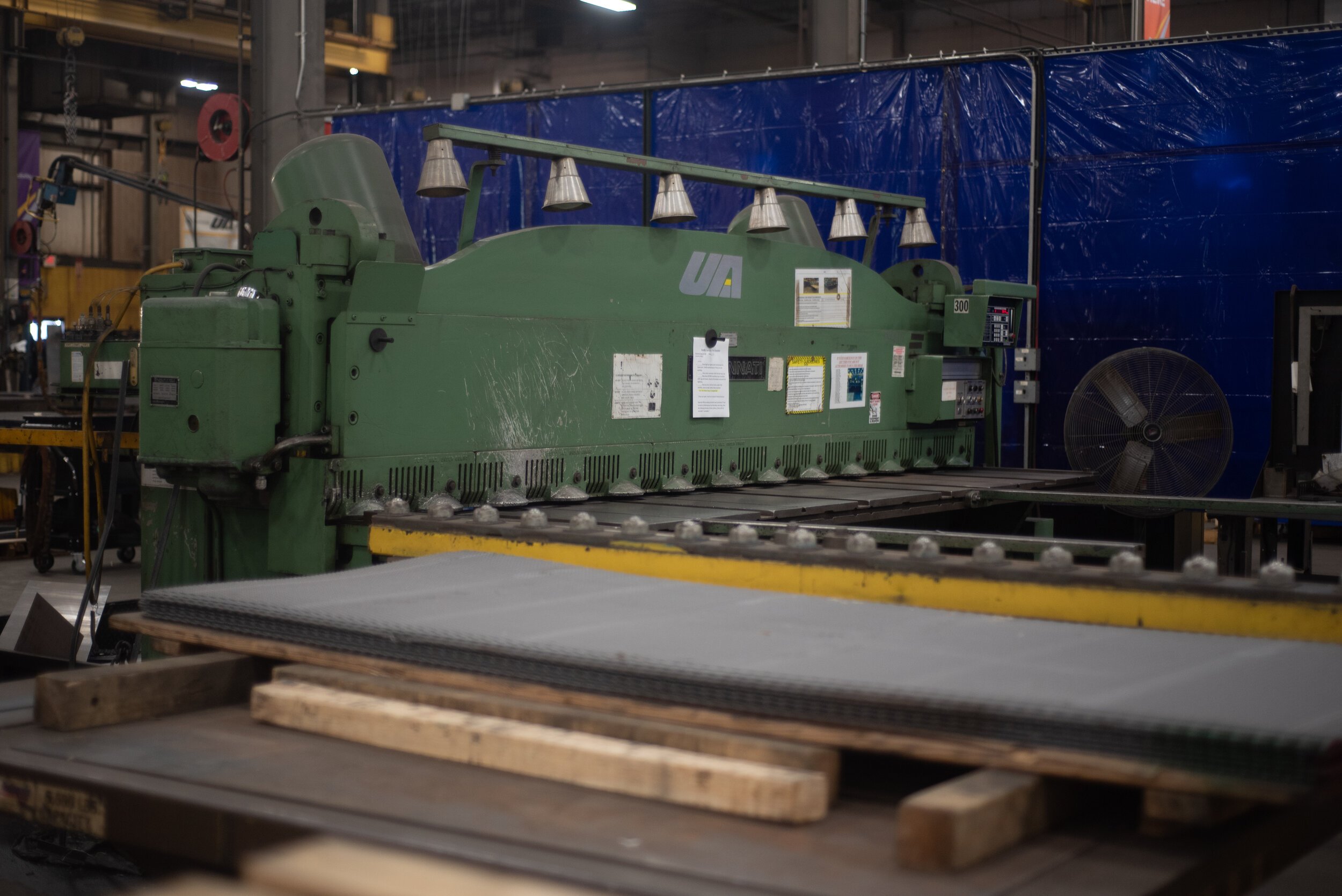
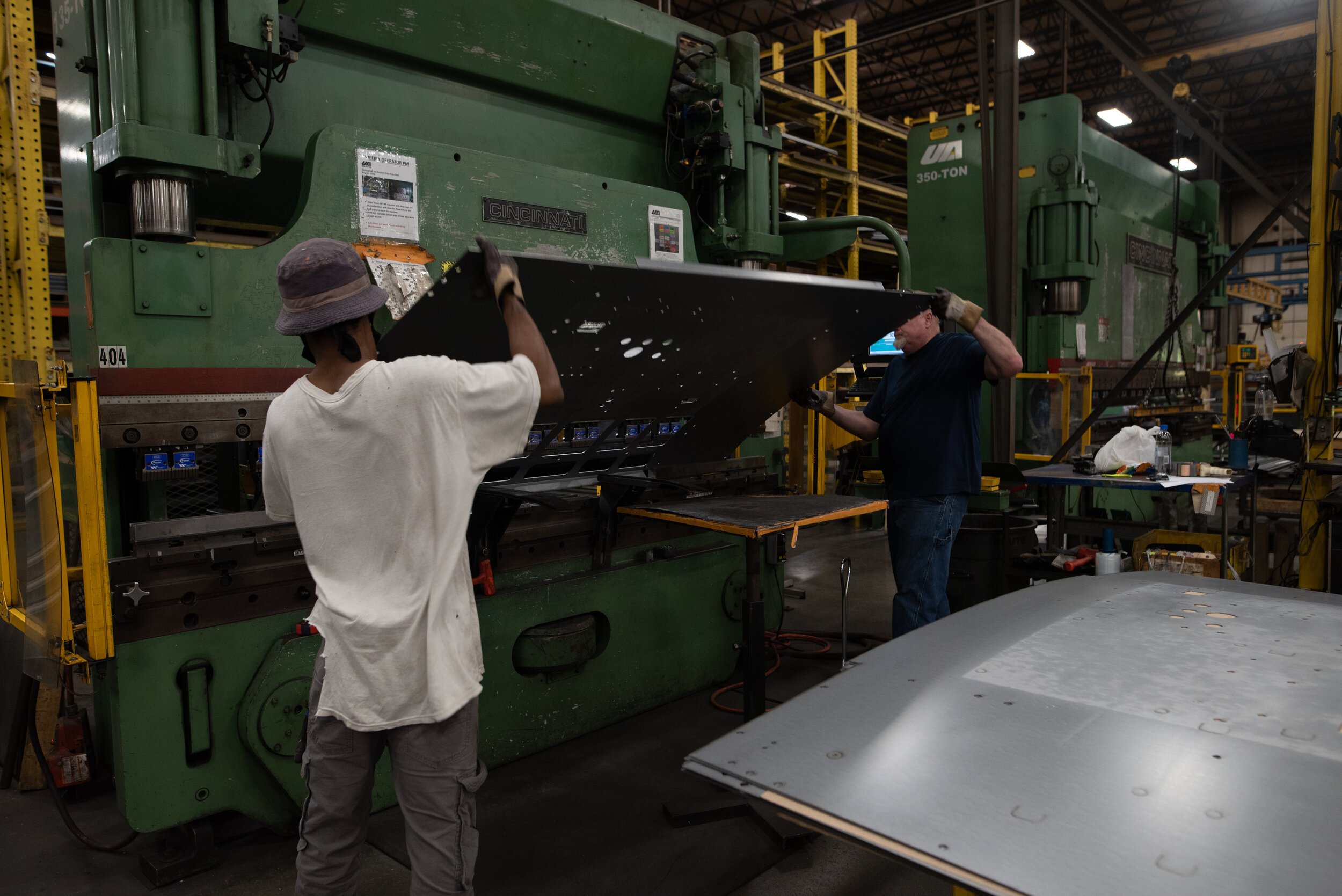
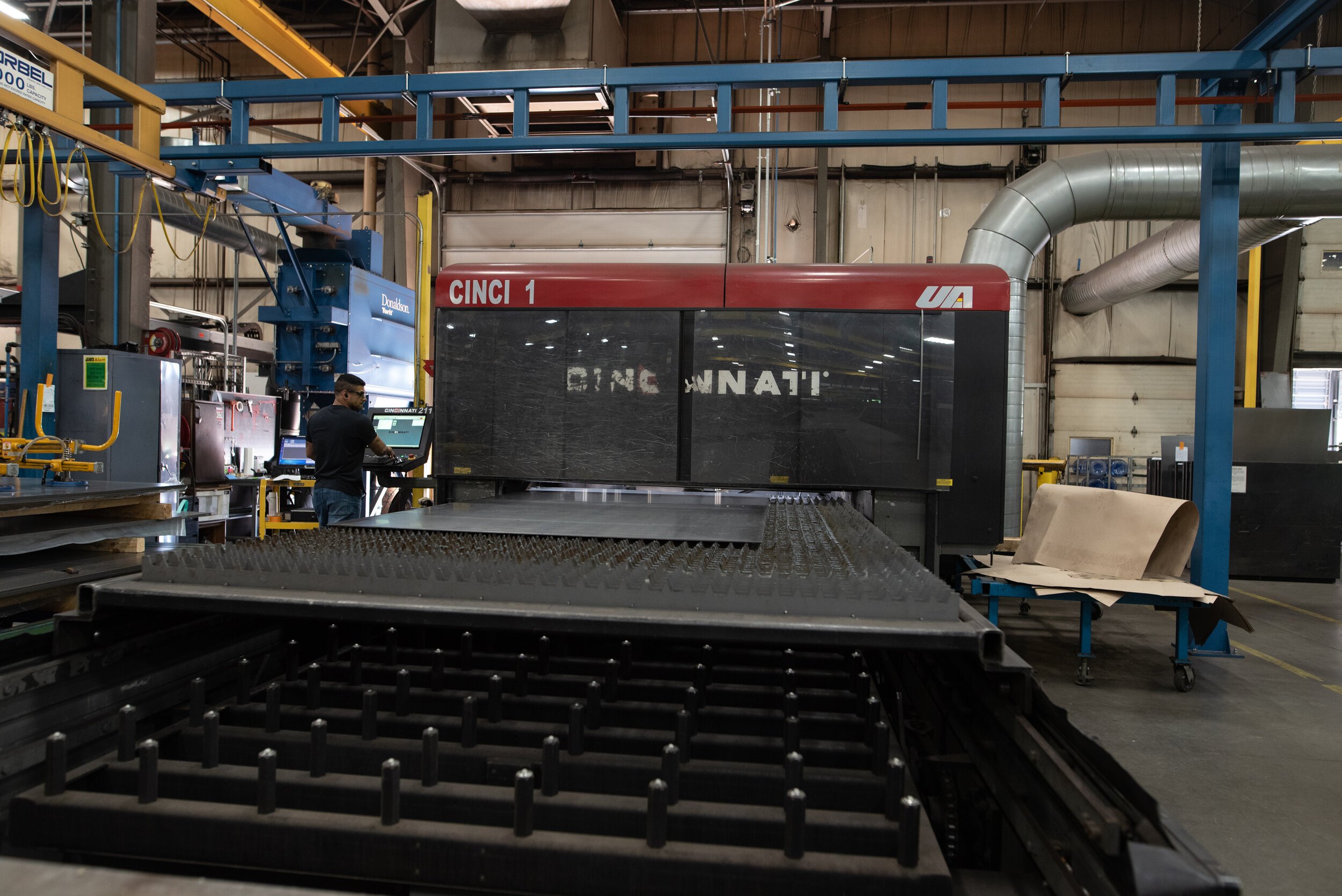
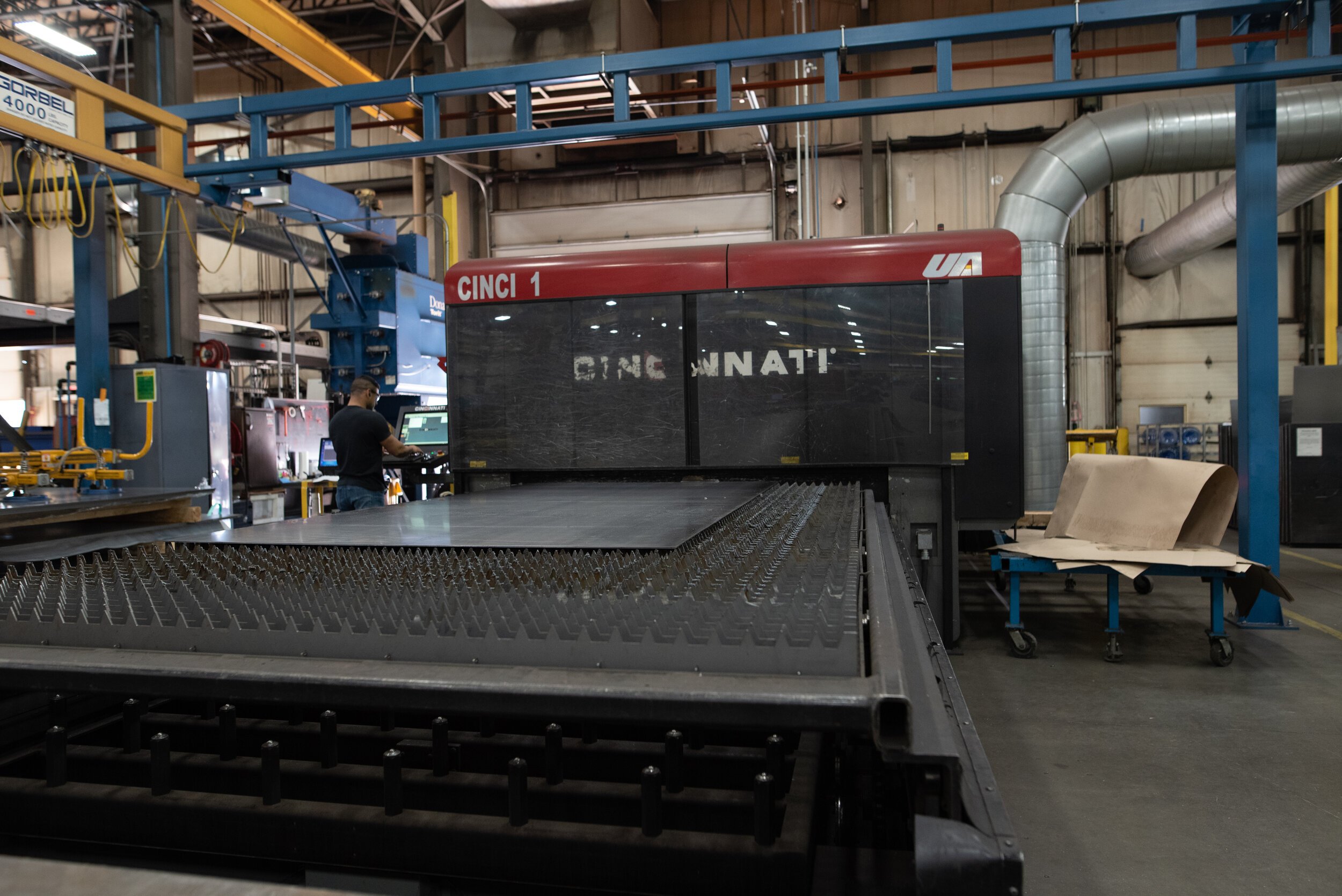
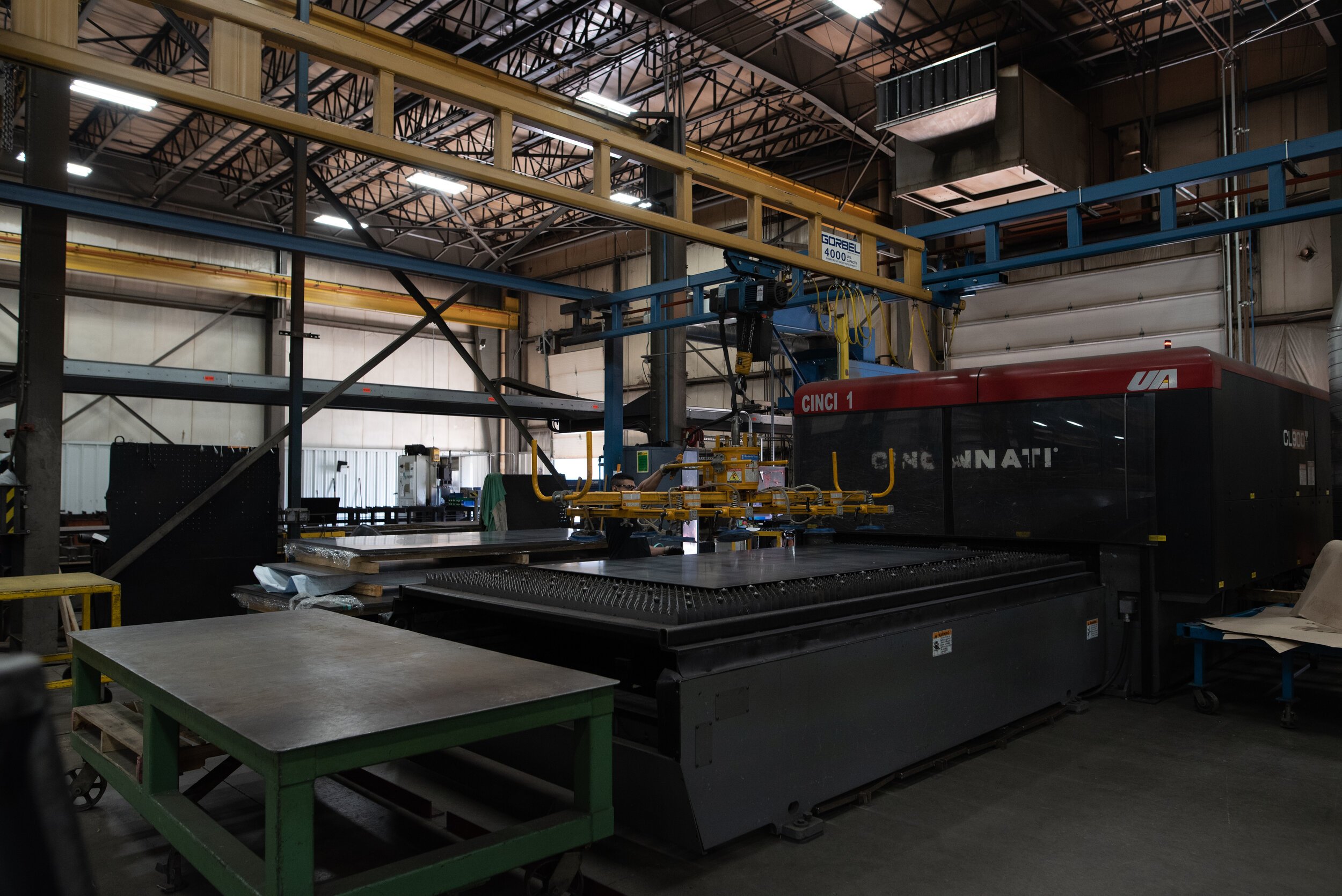
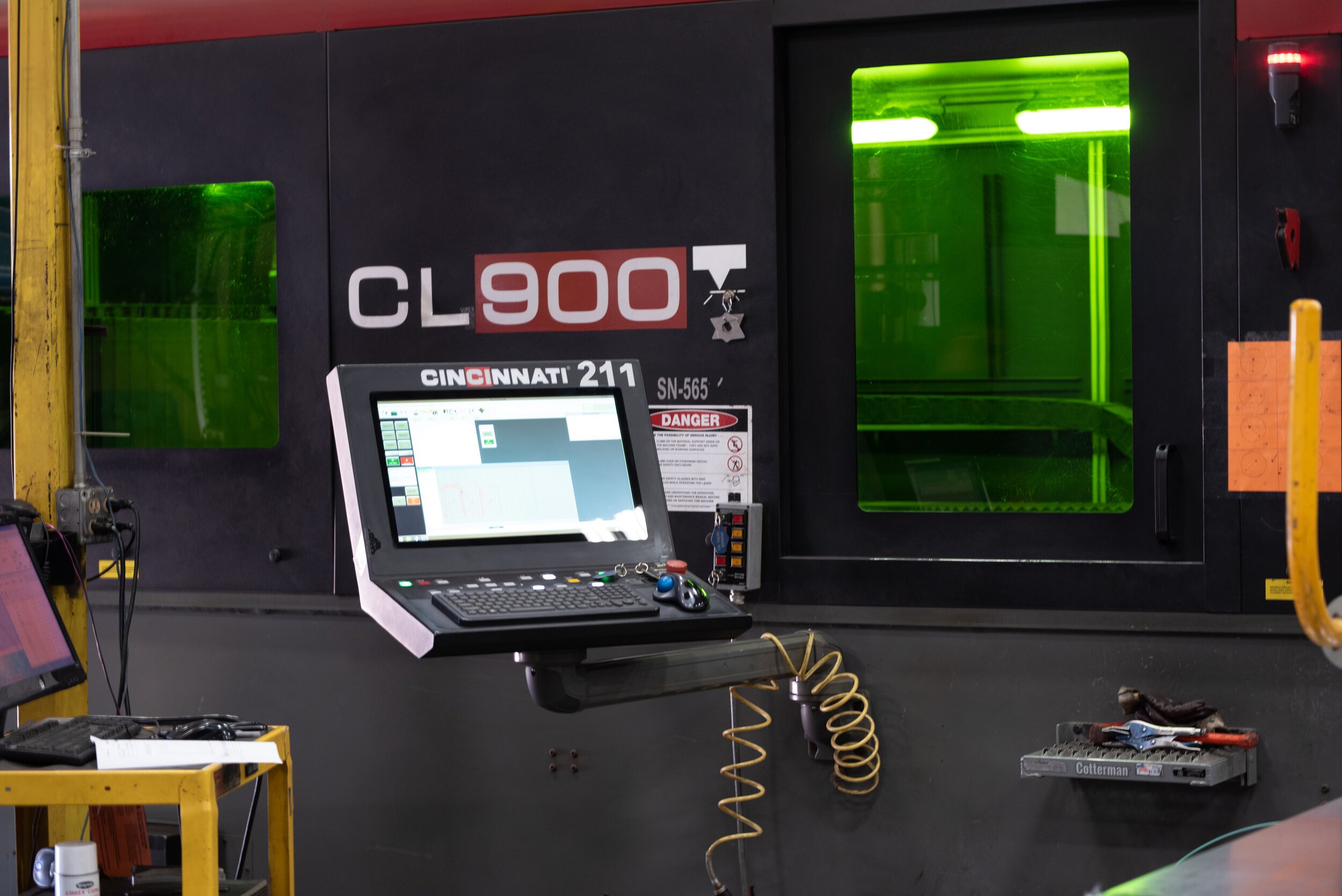

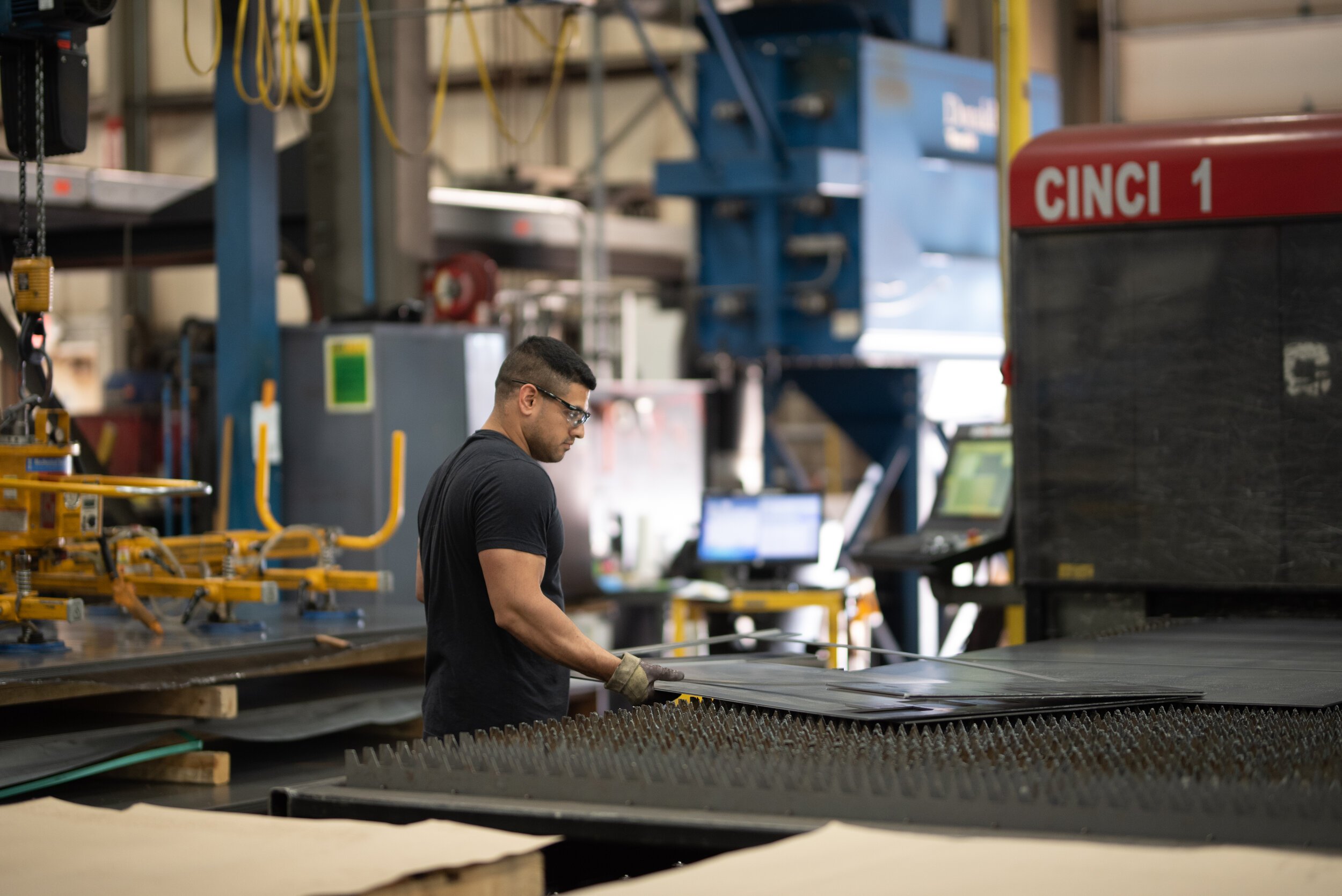
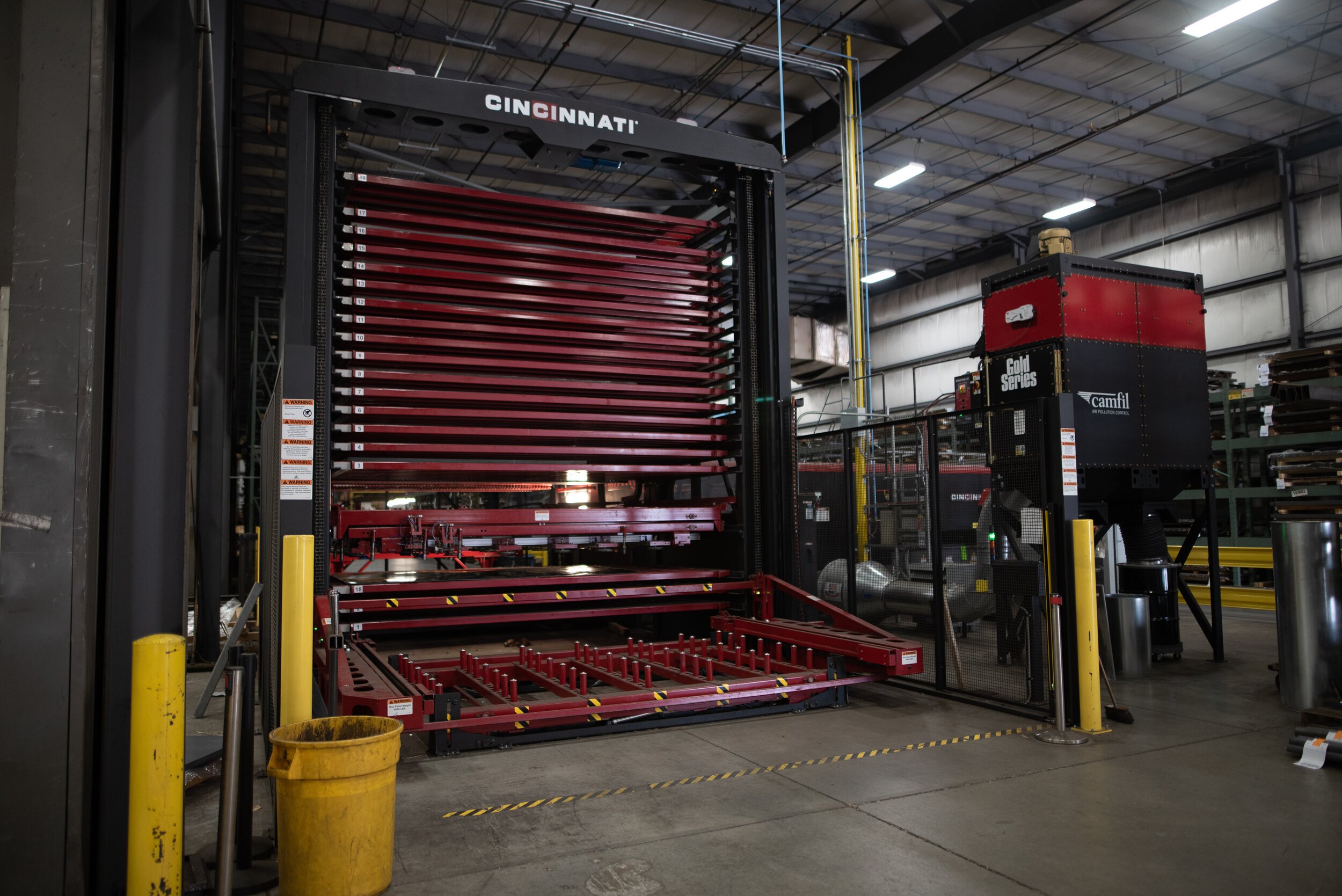
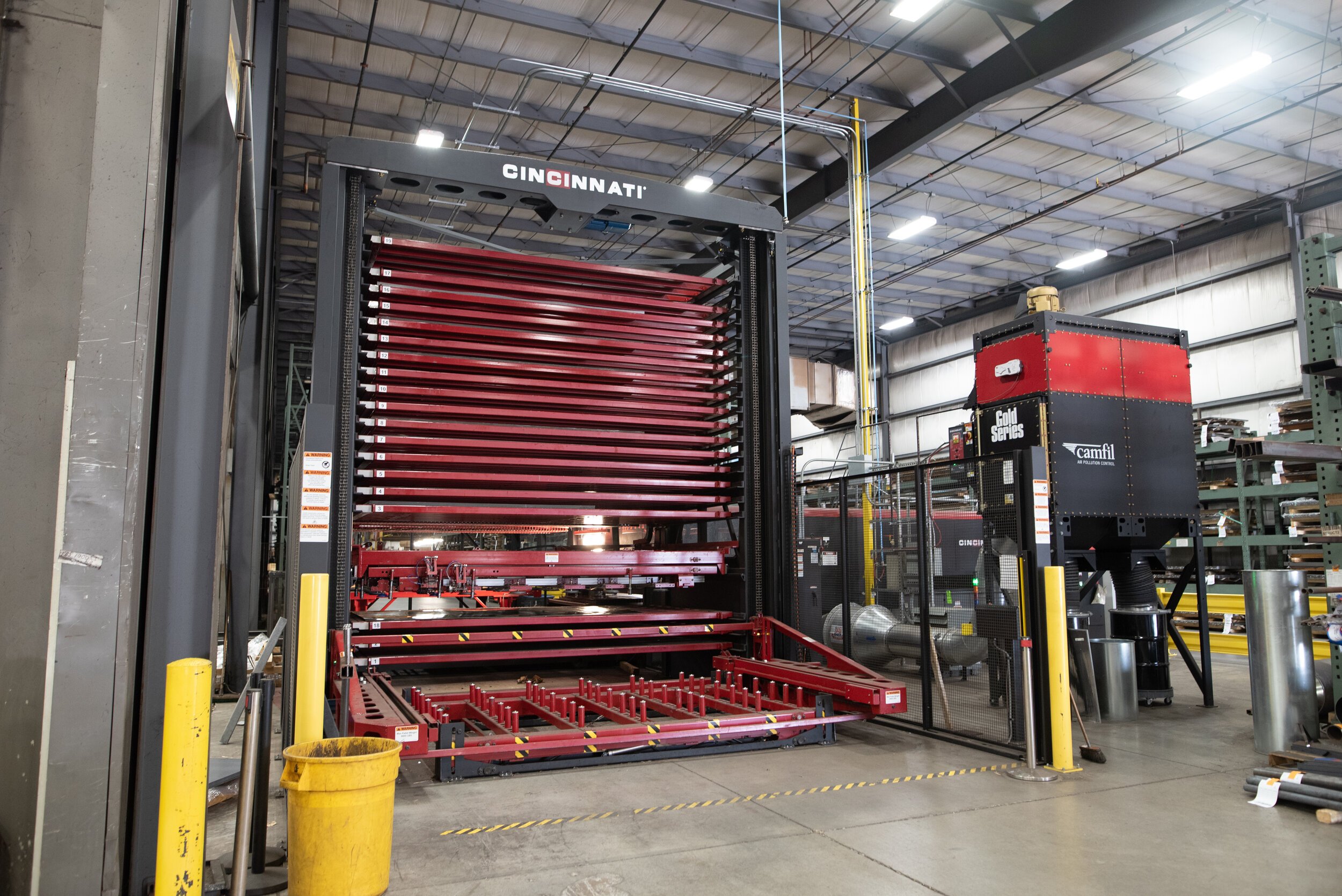
The United Alloy story
If it’s a Fortune 500 OEM in the off-highway equipment industry, chances are United Alloy serves it. The company has crafted a niche thanks to the quality of its power generation products, fuel tanks, enclosures, skid bases and trailers. UA also works with the construction, industrial and agricultural industries on a daily basis.
2020 was on the slower side at UA because of COVID, but business is booming with the recovery well underway. They’re currently running 3 shifts and can’t hire people fast enough. Good problem to have.
On CI machines throughout the shop, UA typically works with 16 gauge to 5/8” steel plates—hot rolled, stainless, galvanized, hot dip galvanized and some aluminum. “What I like most about giving CI machines that material is how reliable they are,” Clark said.
Why UA prefers CI
United Alloy has experience with many machine tool manufacturers, but they’ve always preferred to work with CI. We’ve been working with CI since they got their start in the late 90s. “CI has always been the first choice, as long as they have the piece of equipment that’s right for our job,” Jaynes said.
“We know we’re a demanding customer, and with that demand, CI’s realistic, honest and humble approach suits us perfectly. There will always be problems to solve, and CI isn’t afraid to deal with issues when they come up.”
“At the end of the day, we really just want to trust our partners. Will they be there to help? Will they be there until the end? Cincinnati always is.”
Laser focus
A few years ago, UA realized they needed lasers and automation, and they needed them quickly. The company’s raw material is centered in the middle of the building, so once they opted for CI’s CL-900 laser and MARCH automation tower, the challenge became placing the rack system as close to the raw material bays as possible.
“The vision was to have a streamlined system where the raw material from the trucks would go straight into the MARCH’s racking system,” Clark said. “We didn’t have much floor space to play with, so CI and UA chose to modify a wall in the building, and also come up with modifications to the MARCH system so it could be properly put in place.”
“CI helped us identify the configurations we needed and helped us place the machines on our already crowded floor. Thanks to their help, we ended up with the least amount of modifications to the building and the equipment.”
Looking toward the future
UA tries to promote from within whenever possible, and that means hiring operators and training them to proficiency. “We’ve called on CI’s training team in the past to do that, and their machines and control are easy enough for anyone to pick up on quickly,” Clark said.
“Really, what we like most about CI machines is the reliability. They rarely break down and they always make a good part. The machines themselves are pretty bulletproof.”
For evidence, look no further than UA’s very first CI press brake that they purchased in 1999. It’s still going strong on their floor. If you could use reliability like that, contact us and tell us what you’re looking for.